Generally speaking, holes with a diameter of 0.1mm-1.0mm are called small holes. Most of the materials used in the parts to be machined are difficult-to-machine materials, including cemented carbide, stainless steel and other molecular composite materials, so a variety of small hole processing technologies, methods and equipment have been developed.
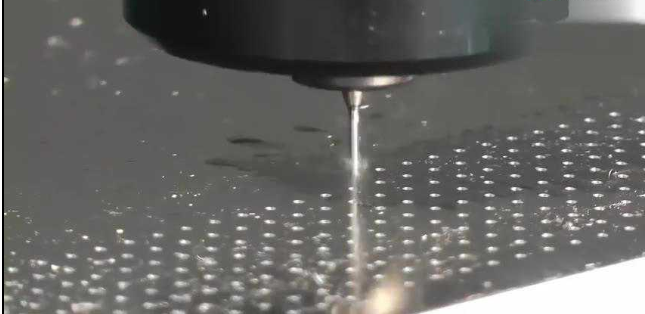
Among them, the method of machining small holes is a traditional machining method with a long history, which is completed by tools or drills, and is currently the most widely used.
In the intensive processing of the above-mentioned ultra-small holes, the moving speed of the drill bit and the drilling speed are very fast, which requires high requirements for the machine tool and the drill bit.
If a worker wants to do a good job, he must first sharpen his tools. When drilling small holes with a machining center, no matter what kind of good machine you use, you have to have a good drill first, right?
Why do people make small holes so fast and well?
One of the key points in small hole machining is chip control and chip evacuation performance.
Chip control: The cutting of the drill is carried out in a hole with a narrow space, and the chips must be discharged through the groove of the drill, so the shape of the chip has a great influence on the cutting performance of the drill. The fine chips block the edge groove, affect the drilling accuracy, and reduce the life of the drill bit; long chips wrap around the drill bit, hinder the operation, cause the drill bit to break or prevent the cutting fluid from entering the hole.
Chip removal performance: If the space of the chip removal groove is not large enough, the chips cannot be discharged smoothly, which will lead to poor drilling accuracy. Therefore, it is necessary to expand the space of the chip flute to achieve barrier-free chip removal and ensure processing stability.
Another key factor in small hole machining is coating technology.
Coatings increase tool wear and heat resistance, thereby extending tool life.
Now, many tool manufacturers will set internal cooling oil holes on the tool holder to help increase the coolant flow and reduce the cooling pressure. When the coolant flow is large, the chips can be discharged more efficiently and stable machining can be achieved.
Of course, there are many more methods besides machining small holes: such as EDM, electron beam, laser, femtosecond laser, chemical etching and plasma cutting, etc.
According to many years of experience, the manufacturing level of a factory can be easily understood by going to the toilet in their factory. This method is quite reliable.
In the process of dealing with factories, each factory will introduce how reliable the quality of its products is and how precise the molds are... You don't need to understand and evaluate from the technical aspect first, and we will talk about it in the bathroom!
Going to some factories, the feeling of going to the bathroom is very pleasant. The environment is bright and clean, elegant and tidy, the toilet is equipped with toilet paper, there is a mirror in front of the sink, hand sanitizer is available, and the faucet has hot and cold water. In contrast, going to the bathroom in some factories is really appalling and indescribable. You know, when you come to the bathroom, you will enter another dark world.
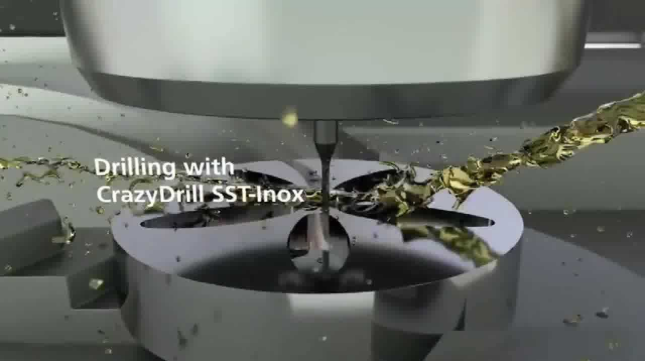
Post time: Oct-24-2022